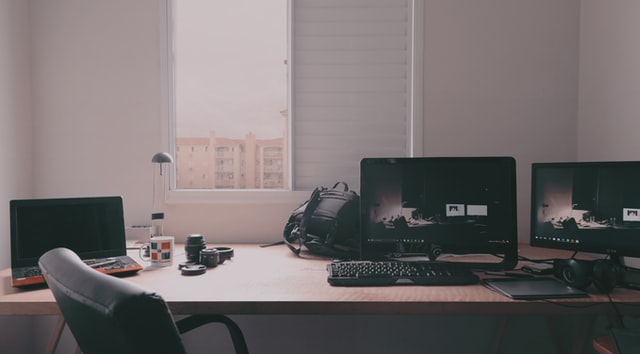
WoW Boosting Explained: A Complete Guide to Fast Progression
With a huge, immersive universe and a sophisticated growth system that keeps players interested for years, the universe of Warcraft (WoW) is one of the most recognizable and long-lasting MMORPGs ever made. However, many players, both new and experienced, may find themselves lagging due to frequent upgrades, expansions, and changing meta-game tactics. The path to the top can be difficult and time-consuming, whether it involves playing in elite PvP tournaments, leveling up rapidly, or obtaining expensive equipment. WoW boosting services are useful in this situation. Boosting is an effective and frequently adjustable way to accomplish in-game objectives and is intended to speed up progress and eliminate tiresome grinding.
First, What Is WoW Boosting?
The term “World of Warcraft boosting” describes a variety of services whereby seasoned players assist others in advancing through the game more quickly. Character leveling, finishing difficult dungeons and raids, earning high Arena ratings, and obtaining coveted in-game items are a few examples of this. In order to accomplish specific goals, a proficient booster usually pilots the client’s account or plays alongside them. Boosting can be bought on a number of platforms, and many businesses provide customized alternatives based on the player’s objectives. Boosting has become a valid component of contemporary MMO culture, even though it may appear like a quick fix, especially in competitive and time-constrained gaming communities.
Available Boosting Service Types
There is no one-size-fits-all approach to WoW boosting. It offers a wide range of services to support various game sectors. Leveling boosting is the most popular kind, in which a booster quickly raises a character’s level from a lower level to the current maximum level. Next are PvE boosts, which concentrate on finishing premium content like Heroic and Mythic raids or Mythic+ dungeons. Players who desire premium gear without having to search for and join progression-oriented groups are particularly fond of these services. Players can obtain exclusive mounts, titles, or transmogs by achieving top Arena or Battleground ratings through PvP boosting.
The Advantages of WoW Boosting Services
There are several benefits to boosting, particularly for players who have time constraints or certain in-game goals. It saves time first and foremost. It can take dozens or even hundreds of hours to sift through content, particularly that which is highly competitive or obsolete. By using practical WoW boosting services, players can avoid the monotonous parts and concentrate on having fun. Second, it grants access to unique rewards, titles, and equipment that might not otherwise be available. This is especially true for content like Gladiator Arena titles or Mythic raids that are gated behind high organizational or skill requirements. Furthermore, coaching is frequently included in boosting services, enabling customers to enhance their performance by observing and picking up tips from professionals.
Hazards and Moral Aspects
WoW boosting has many hazards and limitations despite its advantages. Account security is a big worry, particularly when piloting boosters are used and the user grants access to their account to an unknown individual. This might be against Blizzard’s terms of service, which could lead to suspensions or bans. Additionally, there is the matter of game integrity. Many gamers believe that boosting diminishes accomplishments, erodes the spirit of advancement, and leads to exclusivity or exclusion in endgame material. Furthermore, real-money trading (RMT), which Blizzard actively opposes, has been connected to the boosting market. Players should only employ trustworthy in-game boosting communities or Blizzard-approved strategies, such as those found in the WoW Token economy or guild-organized carry, to reduce these hazards.
How to Pick a Trustworthy Boosting Company
A safe and fulfilling experience depends on choosing the correct boosting provider. Investigate platforms with a track record of success, validated user evaluations, and clear pricing first. Steer clear of dubious websites and offerings that seem too good to be true, as they are frequently frauds or entail account theft. A trustworthy provider will include customer assistance, return policies, an estimated delivery time, and a detailed description of the procedure. Additionally, players need to decide if they want piloted or self-play enhancements. Piloted alternatives are quicker but riskier than self-play, which is typically safer and allows for greater engagement.
For a lot of players who want to improve their gameplay, save time, or access content they otherwise couldn’t, WoW boosting has become an essential component of the World of Warcraft experience. Boosting services provide a useful and effective solution to reach your in-game objectives, regardless of whether you’re a competitive player trying to reach the top ranks or a casual player with restricted hours.